Which Phase is Right for Your Pneumatic Conveying System?
Dense, Semi-Dense or Dilute?
Many industries choose pneumatic conveying systems for transferring dry bulk materials because they are energy efficient and cost effective. However, to achieve maximum results, selecting the correct pneumatic conveying phase for your specific application is essential.
Three Pneumatic Conveying Phases
In a pneumatic conveying system, dry bulk materials are transferred through an enclosed conveying pipeline using the combined force of pressure and gas (commonly air). The difference between the three phases is in how the material flows through the convey line.
- Dense Phase - A relatively low-speed system where the material is not suspended in the air stream. The low velocity of dense phase means less wear and tear on both the system and the materials being conveyed. The velocity is typically set between
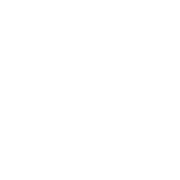 |
| 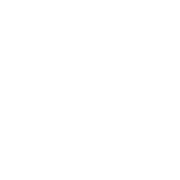 |
Image courtesy of Cyclonaire.
|
400 ft./min. and 1,000 ft./min. Used for low or high rate transfer of abrasive or friable materials. - Semi-Dense Phase - As an intermediary step between dense and dilute phases, the semi-dense phase conveys materials using a medium velocity. Only a portion of the material is suspended in the air stream. Typically set between 1,500 ft./min. and 3,500 ft./min., the velocity ranks higher than dense phase and lower than dilute. Ideal for medium rate transfer of aeratable abrasive or friable materials.
-
Dilute Phase - A high-velocity system where the conveyed material is continuously suspended in the air as it is blown or sucked through the pipeline. Material does not accumulate at the bottom of the convey line at any point. To maintain this suspension, air velocity must be kept, most often, between 5,000 ft./min. and 8,000 ft./min. Used when degradation and abrasive wear are not a factor.
Material Characteristics
Your material's characteristics are key to identifying the right phase for your application. Considerations include:
- Particle Size & Shape determine the flowability and how much air is required to move the material.
- Bulk Density helps determine the design of the pneumatic system and what is required to move the bulk from one place to another.
- Moisture Content affects flowability and can cause materials to pack and clog lines.
- Abrasiveness: The low velocity of dense phase conveying makes it suitable for high-rate transfer of abrasive materials. The medium velocity of semi-dense conveying is best for aeratable abrasive materials. If abrasiveness is not a factor, dilute phase can be considered.
- Friability refers to how easily material crumbles or becomes pulverized. The lower velocities of dense phase and semi-dense phase systems can minimize material degradation,
- Cohesiveness means that the material will adhere to itself under pressure and agglomerate, causing problems within the conveyance lines. This type of material is difficult in all phases of pressure conveying. A vacuum system, dilute or dense phase is often the only choice.
Other factors that influence your selection are
product hygroscopicity, static charge, explosivity, toxicity and melt point.
Testing
TEC engineers can guide you through the selection process. Then, as added insurance, many equipment manufacturers, like Cyclonaire, can follow-up with a full-scale convey test using the same equipment, convey line size, airflow and distance as the proposed system.
For more information, contact your TEC representative.
|
|
|
NEWS
TEC Engineering Welcomes
CYCLONAIRE
A long-established leader in the development of dilute, semi-dense and dense-phase pneumatic conveying systems, Cyclonaire serves the battery, cement, minerals, rail, rubber and manufacturing industries.
A complete line of systems, components and accessories and key innovations like CycloLift®, HC Series conveyors, and DPV-B and DPG-B conveyors keep Cyclonaire at the forefront of pneumatic conveying solutions. Full-scale testing in their own CycloTech™ lab, simulates actual systems, assesses system performance and researches material behavior.
TEC engineers Bob Hodges and Lance Steed represent Cyclonaire in Louisiana, South MS and Southern Alabama.
|
You are shrunk to the size of a candy cane. Your mass is proportionally reduced to maintain your original density. You are then thrown into an empty glass blender. The blades will start moving in 60 seconds.
What do you do?
|
QUOTE OF THE DAY
"The year end brings no greater pleasure than the opportunity to express to you season's greetings and good wishes. May your holidays and new year be filled with joy."
-- Charles Dickens
|
|
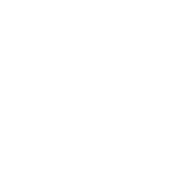 |
|